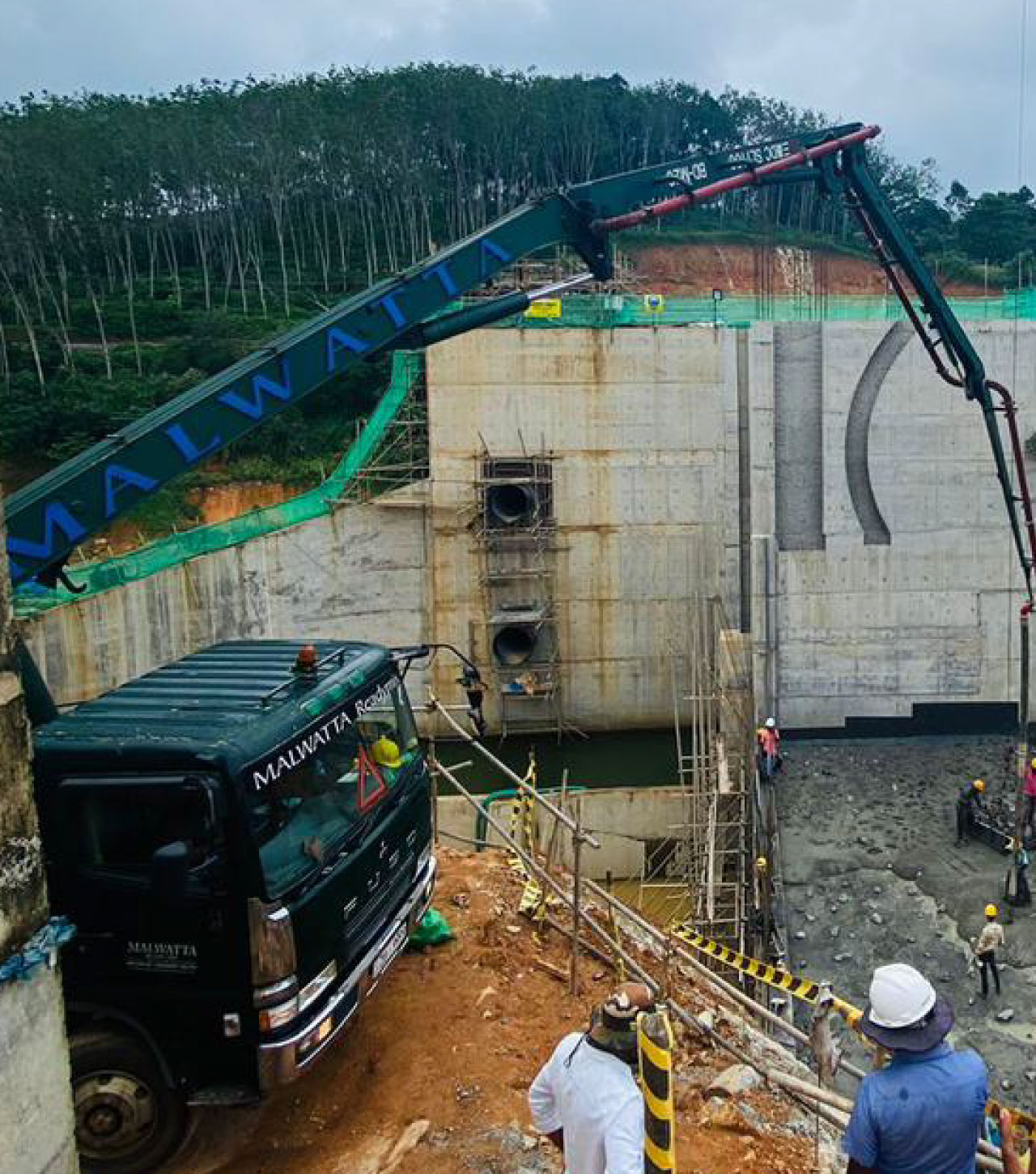
Malwatta Readymix
Gampola Readymix Plant
The company has a fully computerized concrete batching plant in Ulapane. The plant has 30m3 capacities per hour. The plant produces high-quality concrete of each grade with an automatic system.
Warakapola Readymix Plant
The company has a fully computerized concrete batching plant in Warakapola. The plant has 60m3 capacities per hour. The plant produces high-quality concrete of each grade with an automatic system.
BR Number | ISO Certificate No. |
---|---|
PV 122125 | 210928019401 |
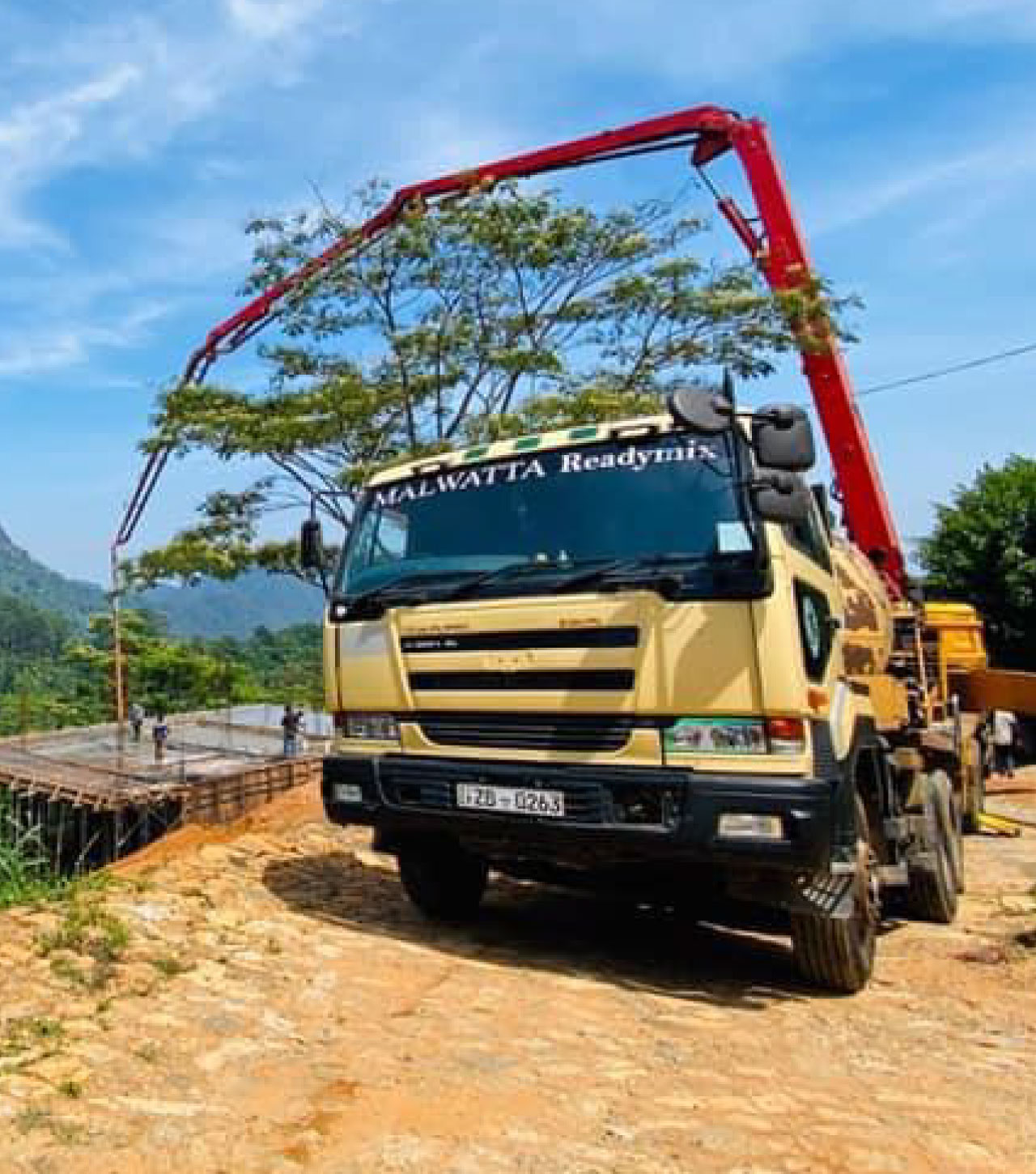
Our Resources
1 | Nissan UD | 5m³ | 05 |
2 | Isuzu | 5m³ | 02 |
3 | Fuso | 5m³ | 01 |
4 | Hino | 5m³ | 02 |
5 | Eicher | 7m³ | 01 |
6 | Isuzu | 1.5m³ | 02 |
ConcretePump car
I. 30m Boom Pump Car
II. 36m Boom Pump Car
III. Concrete Stationary Pump
Wheel Loader
Toyota Wheel Loader -2
Capacity: 1m³
Generators
FGWilson – 2
KVA: 90
Quality Control System
Malwatta ready mix has its own quality control system with highly qualified & experience personals including QA/QC Manger and Lab technicians. There latest and the best equipment are used in the laboratory. It may raise condition and quality of the product what demand the customers.
The laboratory technicians are assigned for their duties on daily basis, in the laboratory and out on field. The routine required for the new raw materials as per ASTM & BS standards are performed regularly and are recorded on the prescribed forms, with supervising and managing of QA/QC Manager.
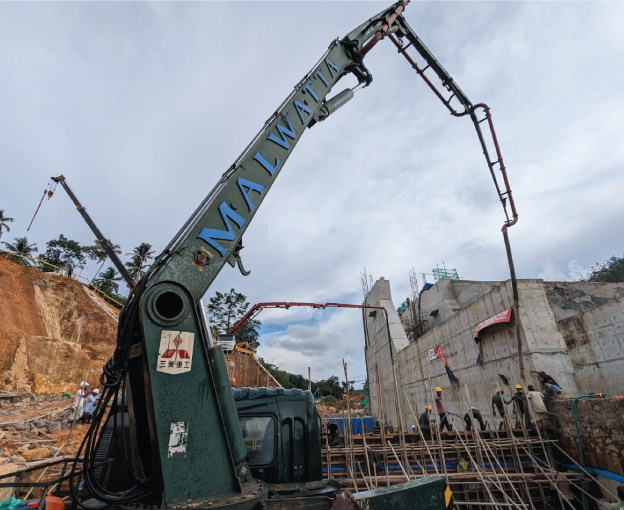
Method Statement
Concrete mix design and constituent material
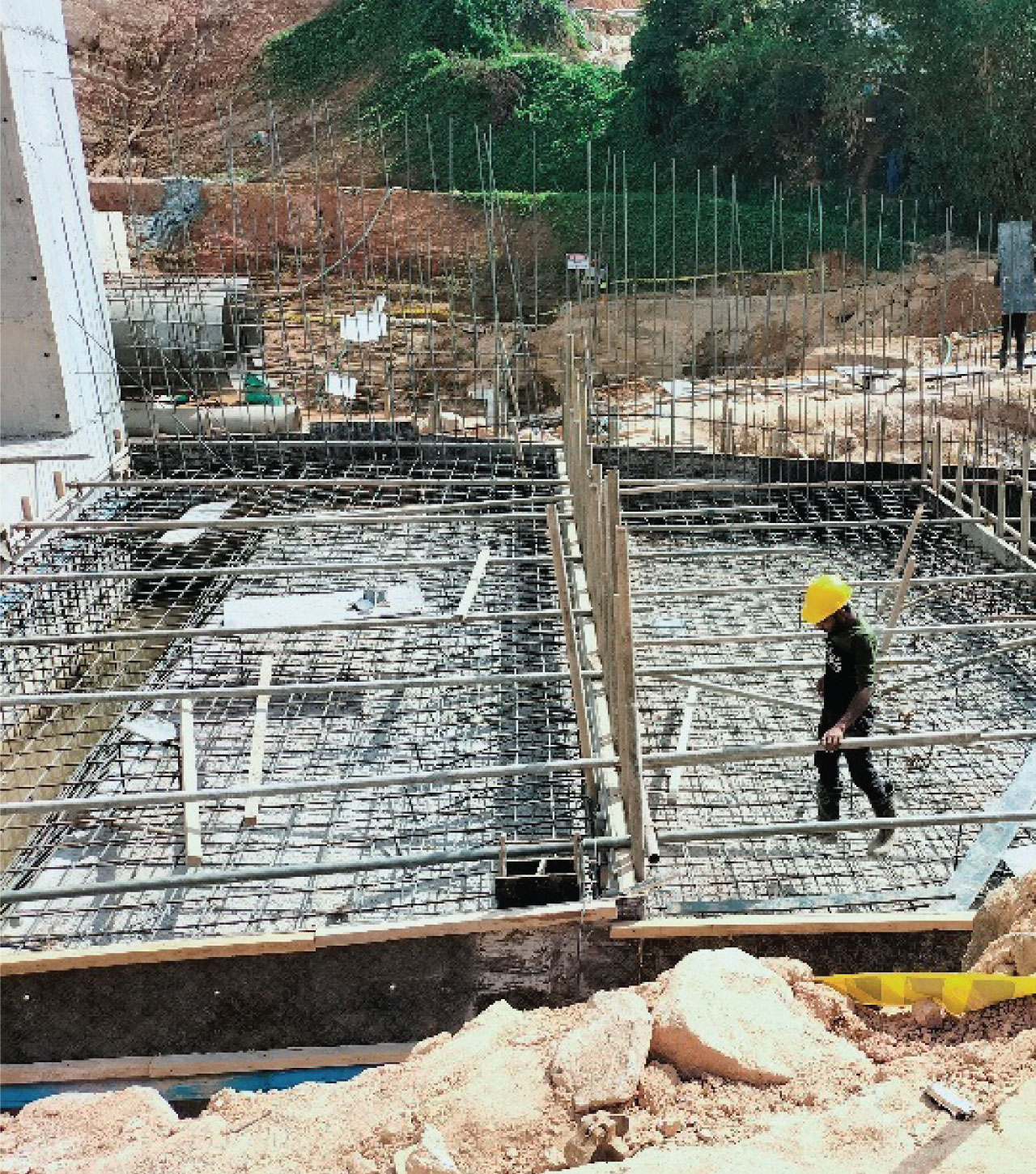
Mix design and pouring method
Mix design were prepared according to the British method of design of concrete mixes & conforming to BS 5328 standard.
According to the documents & the plan it is required several concrete mix designs for footings, columns, beams & slabs. There are 20,25,30,35,40 Grades of ready mix concrete with ‘Tokyo cement’.
For the requirements where the pumping is needed, 150+/-25mm slump is proposed and the water cement ratio was maintained low by using super plasticizer.
Prior to pouring the concrete, has to quality checking (Slump & Concrete cube casting) and taking approval for the concrete. Then concrete can be poured using crane and bucket or using concrete pump.
Coarse and fine aggregates
Coarse aggregate will be crushed stones and fine aggregate in natural river sand and all aggregates will be kept free from clay and dust.
Coarse & fine aggregates will be provided by regular suppliers. Gradation, specific gravity & moisture content will be tested on daily basis.
Coarse aggregate will be sprinkled with water on regular basis to maintain the temperature of batched aggregate at a practically minimum level while maintaining moisture saturated condition.
Water
Water that will be used in concrete will be derived from ground water sources free from contaminants and chemical content (chlorides and other substances) within the standard specified limits.
Admixture
Retarding & plasticizing admixture
– Finex Engineering (PVT) ltd
– Castech Lanka (PVT) ltd
Mixing of concrete
Concrete will be supplied from our own batching plant (wet batched); our batching plants are calibrated at regular intervals to ensure consistency in weigh batched mix proportion.
Transportation of mixed concrete
2.5, 5 & 6 Cubic meter mobile truck mixer will be used for transportation of concrete form the batching plant, it is identified that travelling time in peak traffic hours is approximately 60 minutes and in non-peak traffic situation it will be 40 minutes. To prevent the setting of concrete for approximately 3 hours retarder is used drums of the trucks will be sprinkled with water before loading concrete to the track in order to lower the initial temperature during hot weather.
Placing of concrete
For concrete requirements without pump, slump 75+/-mm mix is proposed and for pumping concretes 150+/-25mm slump mix design is proposed since the high slump is achieved from super plastizer there shall not be any reduction of strength.